| |
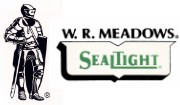
NO. 380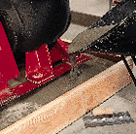
588™
PRECISION GROUT
NON-SHRINK, NON-FERROUS, NON-GASEOUS
Provides excellent workability and high
yields designed to cut placement time costs.
SEALTIGHT 588 PRECISION GROUT is a non-corrosive, non-gaseous, high-strength,
easy-to-use and economical material developed for a wide range of placement
consistencies, excellent workability, adequate placement time and
high-yield cost efficiencies.
Technical Description
SEALTIGHT 588 PRECISION GROUT is a Portland Cement base product. It
is non-corrosive, non-gaseous and provides high density, high initial and
ultimate flexural and compressive strengths. Its high yields help cut in-place
grouting costs. It can be mixed quickly, as needed, on the job-site.
588 GROUT offers exceptional workability and is easily placed by pouring or
pumping. The product is designed to give non-shrink performance under various
conditions, in interior or exterior applications.
Uses
588 is suggested for precision grouting of machinery bases,
generators, rolling mills, punch presses, compressors, etc.; structural grouting
of precast columns, steel columns, crane rails, precast beams, etc.; anchoring
of guard rails, sign posts, bridge seats, anchor bolts, guide wires, dowels,
etc.
Features and Benefits
 | High-flow, high-density, high initial and ultimate
flexural and compressive strengths
 | Non-shrink performance under various conditions, in
interior or exterior applications
 | Joins, supports and anchors...a multiplicity of uses
 | Quickly and easily placed by pouring or pumping
 | Mixes quickly on the job site as needed
 | Offers exceptional workability and high grout
yield...cuts overall grouting costs
 | Resists most oils, gasoline, water, solvent and alkalis
 | Extendable up to 50%
 | Chloride-free
 | No site batching required for consistent results |
| | | | | | | | |
Application Tools

Mortar Mixer
Rubber-Tipped Blades |

Wheelbarrow |

Shovel |
Application
All grouting should be done using
established procedures according to American Concrete Institute recommendations:
ACI 351.1R-93 "Grouting for Support of Equipment and Machinery"
SURFACE PREPARATION: All grout surfaces must be clean, dry and completely free
of laitance, oil, grease, other coatings and any other contamination. Unsound
concrete must be chipped out, leaving surface level, but rough. Grout area
should be saturated with water 12-24 hours prior to grouting. Remove all excess
water before placing grout. Surface should be saturated, surface dry (SSD).
FORMING: Method of forming must provide for rapid, continuous grout replacement.
For pouring, allow a minimum clearance of 3" for entry and 6" minimum
grout "head". Forming must also provide for venting to avoid
entrapment of air. Provide 1/2" minimum form clearance on all sides and
1" clearance for "head".
MIXING: Small quantities of 588 GROUT may be hand mixed in a concrete mixing pan
until lump-free.. For large quantities and continuous pours, mix using a mortar
mixer with rubber-tipped blades or appropriate grout pump for a minimum of 5
minutes. Use minimum water required to produce desired placement consistency.
Use 6.5 pts. (3.1 liters) of water per bag of grout for plastic consistency;
7.25 pts. (3.4 liters) for medium flow (pourable) and 8.25 pts. (3.9 liters) for
high flow.
Mix in 2 steps: Add 2/3 of water requirement...add grout...after partial mixing,
add remainder of water for desired consistency. Thoroughly mix total quantity
for 2 to 3 minutes. Do not mix more than can be placed in 30 minutes.
PLACEMENT: 588 Precision Grout is easily placed by pouring or pumping;
compaction can be accomplished by rodding or light vibrating. Place grout on one
side, flowing to opposite and adjacent sides to avoid entrapment of air. When
necessary, provide vent holes. Grout "head" and excess grout may be
removed after initial set.
CURING: Forms may be removed after grout has hardened to an initial set, usually
within 4 to 6 hours. At this point, make final finish. Prevent rapid loss of
water by covering with wet burlap during first 48 hours or apply appropriate
SEALTIGHT Curing or Curing and Sealing Compound. (We suggest SEALTIGHT 1640-White
or CS-309-1315).
Cost reductions are realized by extending with clean, 3/8" (9.5mm) pea
gravel. In applications where grout thickness is to be 2" to 5" (50 to
130mm), up to 25% of aggregate, based on weight of grout, may be added. For
thicknesses over 5" (130mm) up to 50% of aggregate may be added. Such
additions may be made to the flowable mix.
Packaging
50 lb. (22.7 kg) moisture-resistant polyethylene bags
Specifications
Corps of Engineers Specification: CRD-C 621
USDA Accepted
ASTM C 1107
Yield
Each 50 lb. (22.7 kg) bag yields 0.43 to
0.64 cubic feet (0.0122 cubic meters) of in-place grout using the median water
ratio level, dependent upon rate of extension.
Precautions
Read and follow application information and precautions. Refer to Material
Safety Data Sheet for complete Health and Safety Information.
TYPICAL PROPERTIES
Technical Data; Evaluations made in
accordance with CRD-C 621 '80
Consistency
per ASTM C 827-95a
Mix Ratio per 50 lb. bag
Flow per ASTM C 230-90
5 Drops/Flow Table
Flow per ASTM C 939-94a
Flow Cone |
Plastic
6.5 Pints
(3.07 Liters)
110% |
Flowable
7.25 Pints
(3.43 Liters)
130% |
Fluid
8.25 Pints
(3.89 Liters)
28 Secs. |
SET TIME per ASTM C 192-92 |
Initial Set |
1 hr. |
3 hrs. |
5 hrs.. |
Final Set |
3 hrs.. |
5 hrs.. |
7 hrs. |
EXPANSION
Age:
24 hours
3 days
7 days
28 days |
0.13%
0.16%
0.17%
0.17% |
0.10%
0.13%
0.13%
0.14% |
0.02%
0.04%
0.05%
0.06% |
SHRINKAGE % |
NONE |
NONE |
NONE |
COMPRESSIVE STRENGTH |
AGE
1 day
3 days
7 days
28 days |
psi (MPa)
4,233 (29.2)
6,308 (43.5)
7,987 (55.1)
10,792 (74.5) |
psi (MPa)
3,183 (22.0)
5,167 (35.7)
6,250 (43.1)
8,008 (55.3) |
psi (MPa)
1,575 (10.9)
3,617 (25.0)
4,742 (32.7)
5,900 (40.7) |
* All application and
performance properties are typical for this material.
** These values should only be used as a guide for determination of
suitability by qualified persons. |
Pullout and
Torque Tests |
Reinforcing Bar Pullout |
No. 6 deformed rebars
grouted in 2.25" (57.2mm) diameter and 6" (152.4mm) deep core
in 4,000 psi (27.6MPa) concrete. Load applied at a rate of
0.25"/min. (6.35mm/min.). |
Average load: 18,000 lbs.
(124.2 MPa) for concrete failure after 7 day cure |
Machine Bolt Pullout |
3/4" (19mm) diameter
machine bolts (without washers) grouted in 2.25" (57.2mm) diameter
and 6" deep core in 4,000 psi (27.6 MPa) concrete. Load applied at
a rate of 0.25"/min. (6.35mm/min.). |
Average load: 20,630 lbs.
(142.3 MPa) for concrete failure after 7 day cure |
Machine Bolt Torque |
3/4" (19mm) diameter
machine bolts (without washers) grouted in 2.25" (57.2mm) diameter
and 6" deep core in 4,000 psi (27.6 MPa) concrete. Load applied at
a rate of 0.25"/min. (6.35mm/min). |
Average torque values in
excess of 425 ft./lbs.
(5.8 x 10³ m/kn) |
This material last updated January, 2001.
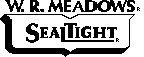
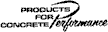
W. R. MEADOWS, INC. warrants that, at the time and place
we make shipment, our materials will be of good quality and will conform with
our published specifications in force on the date of acceptance of the order.
THE FOREGOING WARRANTY SHALL BE EXCLUSIVE AND IN LIEU OF ANY OTHER WARRANTY,
EXPRESS OR IMPLIED, INCLUDING THE IMPLIED WARRANTIES OF MERCHANTABILITY AND
FITNESS FOR A PARTICULAR PURPOSE AND ALL OTHER WARRANTIES OTHERWISE ARISING BY
OPERATION OF LAW, COURSE OF DEALING, CUSTOM OF TRADE OR OTHERWISE. As the
exclusive remedy for breach of this Warranty, we will replace defective
materials, provided, however, that the buyer examine the materials when received
and promptly notify us in writing of any defect before the materials are used or
incorporated into a structure. Three (3) months after W. R. MEADOWS, INC. has
shipped the materials, all our Warranty and other duties with respect to the
quality of the materials delivered shall conclusively be presumed to have been
satisfied, all liability therefore terminates, and no action for breach of any
such duties may thereafter be commenced. W. R. MEADOWS, INC. shall in no event
be liable for consequential damages. Unless otherwise agreed to in writing, no
warranty is made with respect to materials not manufactured by W. R. MEADOWS,
INC. We cannot warranty or in any way guarantee any particular method of use or
application of the performance of materials under any particular condition.
Neither this Warranty nor our liability may be extended or amended by our
salesmen, distributors or representatives, or by our distributor's
representatives, or by any sales information or drawings.
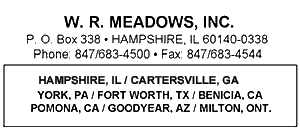
|