| |
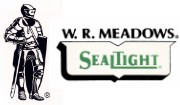
NO. 391S-PD
REZI-WELD™
GEL PASTE STATE
CONSTRUCTION EPOXY
DESCRIPTION
SEALTIGHT REZI-WELD GEL PASTE STATE is a high
viscosity, two-component, rapid setting epoxy compound designed for general
concrete repair work. It is an easy-to-mix, easy-to-apply non-sag gel ideal for
filling cracks, anchoring dowels, making small patches and general repairs in
horizontal, vertical and overhead concrete surfaces.
When used as an adhesive, SEALTIGHT REZI-WELD GEL PASTE
STATE fills all voids between the surfaces to be bonded, whereas a liquid epoxy
adhesive might run out and reduce the bond area. SEALTIGHT REZI-WELD GEL PASTE
STATE is also suitable for surface sealing prior to pressure injecting.
SEALTIGHT REZI-WELD GEL PASTE STATE is a moisture
insensitive, high-modulus, high-strength, non-sagging and trowel-grade epoxy. It
is VOC compliant and color coded to help assure proper mixing.
PHYSICAL PROPERTIES
Consistency: ASTM C 881 |
PASS |
Slant Shear Bond Strength ASTM C 882
@ 2 Days
@ 14 Days |
3,000 PSI (19.3 MPa)
3,800 PSI (20.7 MPa) |
Absorption ASTM D 570 |
0.84% |
Heat Deflection Temperature ASTM D 648 |
125ºF (51.7ºC) |
Linear Coefficient of Shrinkage ASTM D
2566 |
|
Compressive Yield Strength: ASTM D 695
@ 7 Days |
10,500 PSI (72.4 MPa) |
Compressive Modulus: ASTM D 695
@ 7 Days |
500,000 PSI (3,448 MPa) |
TECHNICAL DATA
COLOR: |
PART A WHITE
PART B BLACK |
MIX RATIO |
1:1 By Volume |
POT LIFE |
5-10 Minutes at 77ºF |
CURE TIME |
7 Days at 77ºF |
SHELF LIFE |
1 Year |
COVERAGE |
1 Gallon Neat yields 231
cubic inches |
PACKAGING
10 Gallon (37.85 liter) Units
20 Ounce (591 milliliter) Unitized Cartridges
SPECIFICATIONS
ASTM C 881 |
Type I, II, IV, & V |
|
Grade 3, Classes B & C |
AASHTO M 235 |
Type I, II, IV & V |
|
Grade 3, Classes B & C |
I.C.B.O.-E.S. |
E.R. #5000 |
City of Los Angeles |
R.R. #25247 |
SURFACE PREPARATION
All surfaces to be bonded must be free of standing water and completely clean of
dirt, rust, curing compounds, grease, oil, paint, and unsound materials which
would prevent a solid bond. Concrete should be cleaned by light mechanical
abrading to form a sound surface. Vacuum or blow away dust with oil-free
compressed air. Smooth surfaces, such as wood, require sanding or other
mechanical abrasion. Exposed steel surfaces should be sandblasted and vacuumed
clean . . . if not possible, degrease the surface and use sandpaper or a wire
brush to reveal continuous, bright metal.
MIXING
Condition all components to 60º-85ºF for 24 hours prior to use. Pre-mix each
component. Mechanically mix at slow speed (600-900rpm) using a drill and Jiffy®
Blade or drum mixer for 3 minutes or until completely mixed while scraping the
sides to ensure complete blending of components. The mixed product should be
uniform gray in color and not show streaks. Avoid air entrapment. Mix only very
small quantities by hand for a minimum of 3 minutes or until sufficiently
blended together using the supplied stirring stick. Scrape the sides of the
container to ensure complete blending of the components. Mix only the amount of
epoxy that can be applied within the product’s potlife. Potlife will decrease
as the ambient temperature and/or mass size increases.
APPLICATION
METAL ANCHORS IN PREFORMED HOLES IN CONCRETE:
Preformed holes should be approximately ¼" (6.35mm) larger in diameter
than the anchor bolt diameter. The depth of the hole should be 10-15 times the
bolt diameter. Fill the hole from the bottom up, about half way with mixed epoxy
and place the bolt, dowel or rebar. Top off with more epoxy and finish. All
anchoring and doweling configurations must be approved or designed by an
engineer.
CRACKS IN VERTICAL OR OVERHEAD STRUCTURES:
For non-moving cracks and joints, use a trowel
to apply the paste full depth and strike off flush at the surface in a single
pass. For structural crack injection repairs, use a dual-component gel pump.
PATCHES IN CONCRETE STRUCTURES: GEL PASTE makes a high-strength material
for patching, topping, grouting and repairing spalls and other defects in
concrete. Average thickness of the patch or topping should be no greater than ¼
to ½" (6.35 to 12.7mm) per lift.
SURFACE SEALING: Apply
mixed epoxy over entire length of crack to be pressure injected. Ensure complete
encapsulation to avoid leaking. Adjacent concrete surfaces must be mechanically
abraded to ensure a proper bond. Allow for suitable cure time prior to
injecting.
OTHER BONDING: To bond
cured concrete or metal to concrete, apply a layer no less than a 1/64"
(.40mm) to the prepared surface and join immediately. No firm clamping pressure
is necessary beyond what will hold parts in place. When bonding fresh concrete
to cured concrete, apply GEL PASTE at approximately
85-100 ft²/gal. (2.1-2.4 m²/L). NOTE: Cured concrete surfaces to be bonded
should be at least 28 days old.
CLEANUP: Tools and equipment should be cleaned immediately with Toluene
or Xylene. Clean equipment away from heat, sparks and open flame and avoid
breathing vapors or allowing epoxy-containing solvent to contact skin. Should
this material come in contact with the skin, wash thoroughly with soap and
water; not solvent.
LIMITATIONS/PRECAUTIONS
Not recommended for use when the concrete
temperature has been below 40ºF for the past 24 hours. Do not thin with
solvents or use to seal cracks under hydrostatic pressure. Do not warm epoxy
over direct heat . . . use the double-boiler method or store material in warm
room for 24 hours prior to application. Unused epoxy will generate excessive
heat, especially in large quantities. Unused epoxy should be mixed with dry sand
in the container to help lower the heat.
Refer to Product Material Safety Data Sheet for complete
Health and Safety Information.
This material last updated December, 2001.
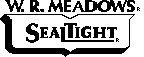
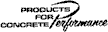
LIMITED WARRANTY
W.R.MEADOWS,INC. warrants that at the time and place we make shipment, our
material will be of good quality and will conform with our published
specifications in force on the date of acceptance of the order. Read complete
warranty. Copy furnished upon request.
Disclaimer
The information contained herein is included for illustrative purposes only, and
to the best of our knowledge, is accurate and reliable. W.R.MEADOWS,INC. cannot
however under any circumstances make any guarantee of results or assume any
obligation or liability in connection with the use of this information. As
W.R.MEADOWS, INC. has no control over the use to which others may put its
product, it is recommended that the products be tested to determine if suitable
for specific application and/or our information is valid in a particular
circumstance. Responsibility remains with the architect or engineer, contractor
and owner for the design, application and proper installation of each product.
Specifier and user shall determine the suitability of
products for specific application and assume all responsibilities in connection
therewith.
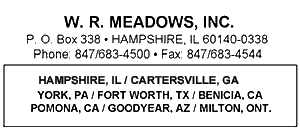
|