| |
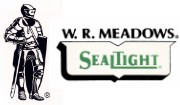
NO. 720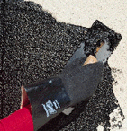
SEALMASTIC™
SOLVENT DAMPPROOFINGS
Three dependable application grades to
meet your specification requirements.
SEALTIGHT SEALMASTIC Dampproofing Coatings are available in 3 dependable
application grades for spraying, brushing or troweling.
Technical Description
SEALMASTIC Solvent-Type Dampproofings are asbestos-free,
fibered-asphalt compounds containing an exclusive wetting agent to convert a
naturally hydrophobic surface to a hydrophilic surface to assure proper coating
adhesion. Both the brush-on and trowel applied coatings are flexible and will
span small holes and hairline cracks. All 3 grades withstand temperature changes
and will not crack under normal expansion or contraction. The 3 types offered
are:
SPRAY-MASTIC Dampproofing, a non-fibered asphalt compound for use where spray
application is desired.
SEMI-MASTIC Dampproofing, a brush or spray-on fibered
asphalt compound designed to protect exterior below-grade masonry walls.
TROWEL-MASTIC Dampproofing, a trowel-applied,
heavy-bodied, fibered asphalt compoumd for exterior, below-grade masonry wall
surface applications. It is recommended to protect porous or irregular surfaces.
All SEALMASTIC products meet the VOC content of 500 g/L
for Bituminous Coatings and Mastics as required by U.S. EPA Architectural
Coatings Rule.
Uses
SEALMASTIC Solvent Type Dampproofing Coatings are ideal for
reducing dampness and moisture infiltration through foundation walls, footings,
retaining walls, parapets, fire walls, tanks, culverts, cisterns and bridge
abutments. They are also applicable for stone-backing, above-grade cavity wall
applications and below-grade masonry wall dampproofing.
Features and Benefits
 | Ready-to-use...no heating or thinning required...dries
rapidly
 | Fast and economical way to protect concrete and masonry
foundation walls from moisture penetration
 | Easy-to-apply...available in spray, brush or trowel
grades to meet a broad application range
 | Three application grades available for maximum
versatility
 | VOC compliant... meets the U.S. EPA Architectural
Coatings Rule requirements |
| | | |
Application Tools

Trowel |

Electric Drill with Jiffy Mixer |

Soft Bristle Brush |

Ratio Pump |

Wire Brush |
Maintain Energy Efficiency
SEALTIGHT Products applied for thermal and moisture protection help prevent
moisture or vapor penetration into the other systems of the structure. These
products play a key role in maintaining the structure's energy efficiency.
Application
MIXING: For Spray-Mastic or Semi-Mastic,
stir the contents in the container thoroughly prior to applying with a soft
bristle brush or suitable spray equipment. When applying Spray-On Dampproofings,
use a Graco 9:1 ratio pump or equal, capable of delivering 3 to 5 gallons per
minute (11.36 liters to 18.93 liters), and a Polegun with a 1/8" (3.18mm)
to 1/4" (6.35mm) tip. A 3/4" I.D. (19.05mm) material hose and a
1/2" I.D. air hose from the pump to the gun is recommended for most
applications. Apply SEALMASTIC Dampproofings to clean, dry surfaces at
temperatures above 40ºF (4ºC). Apply in a continuous, unbroken film, free of
pinholes and over any exposed footings, slots or grooves, etc.
NOTE: Fillers, extenders and additives in concrete mixes can produce a higher
than normal porosity and as a result, additional coverage coats may be required.
SURFACE PREPARATION: All surfaces to be coated must be
thoroughly cleaned of all scale, loose mortar, rust, dirt, oil, grease and other
foreign matter. Use a wire brush, sandblast or other methods in keeping with
good construction practices. Before product application, fill voids, cracks and
holes in concrete with cement mortar and allow to dry. Dusty or porous masonry
must be primed with asphalt primer and allowed to dry thoroughly before applying
dampproofings.
Do not apply when the temperatures below 35ºF (2ºC) are anticipated. Do not
apply in rain or when rain is threatening. For added protection against
backfilling damage, install SEALTIGHT PROTECTION COURSE after the damproofing
has dried. Backfill immediately. SEALMASTIC Damproofings should not be used in
areas subjected to prolonged exposure to sunlight.
POROUS SURFACES, i.e. concrete block:
 | For moderate conditions, apply a heavy coating of
cement mortar and one coat of SEALTIGHT SPRAY-MASTIC, SEMI-MASTIC or
TROWEL-MASTIC 1/16" (1.59mm) wet film thick. For added protection,
apply a second coat 1/16" (1.59mm) wet film thick.
 | For severe conditions or for added protection, wait 24
hours before applying a second coat 1/16" (1.59mm) wet film thick of
SPRAY-MASTIC, SEMI-MASTIC or TROWEL-MASTIC. Within four hours of the last
coat, press glass fabric into the mastic, overlapping each piece three to
four inches. Allow 48 hours more before backfilling. |
|
DENSE CONCRETE SURFACES:
 | For moderate conditions, generally 1 coat of
SPRAY-MASTIC, SEMI-MASTIC or TROWEL-MASTIC 1/16" (1.59mm) wet film
thick is recommended. If SPRAY-MASTIC is used, 2 coats are preferable. Allow
12 hours between coats.
 | For severe conditions, or for added protection, apply 2
coats of SPRAY-MASTIC, SEMI-MASTIC or TROWEL-MASTIC to a total thickness of
1/8" (3.18mm). If desired, glass fabric can be embedded in the first
coat. Allow 24 hours before applying the second coat.
|
|
Packaging
5 gallon (18.93 liter) Pails
55 gallon (208.20 liter) Drums
Specifications
Spray-Mastic
Semi-Mastic
Trowel-Mastic |
ASTM D 4479, Type I
ASTM D 4479, Type I
ASTM D 4586, Type I |
Precautions
Handle as a combustible product.
Read and follow application information and precautions. Refer to Material
Safety Data Sheet for complete Health and Safety Information.
Coverage*
Spray-Mastic
 | Below-grade: First coat, approximately 80 ft.²/gal.
(1.96m²/L).
 | Above-grade: Approximately 100 ft.²/gal. (2.45 m²/L)
per coat.
 | Stone-backing: Approximately 150 ft.²/gal. (3.68
m²/L). |
| |
Semi-Mastic
 | One-coat, approximately 30 ft.²/gal. (.74 m²/L)
1/16" (1.59mm) thick depending on texture and porosity of the surface. |
Trowel-Mastic
 | One-coat, approximately 25 ft.²/gal. (.61 m²/L)
1/16" (1.59mm) thick. |
* All coverage rates are based on wet film thickness.
This material last updated October, 2000.
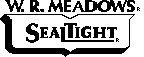
W. R. MEADOWS, INC. warrants that, at the time and place
we make shipment, our materials will be of good quality and will conform with
our published specifications in force on the date of acceptance of the order.
THE FOREGOING WARRANTY SHALL BE EXCLUSIVE AND IN LIEU OF ANY OTHER WARRANTY,
EXPRESS OR IMPLIED, INCLUDING THE IMPLIED WARRANTIES OF MERCHANTABILITY AND
FITNESS FOR A PARTICULAR PURPOSE AND ALL OTHER WARRANTIES OTHERWISE ARISING BY
OPERATION OF LAW, COURSE OF DEALING, CUSTOM OF TRADE OR OTHERWISE. As the
exclusive remedy for breach of this Warranty, we will replace defective
materials, provided, however, that the buyer examine the materials when received
and promptly notify us in writing of any defect before the materials are used or
incorporated into a structure. Three (3) months after W. R. MEADOWS, INC. has
shipped the materials, all our Warranty and other duties with respect to the
quality of the materials delivered shall conclusively be presumed to have been
satisfied, all liability therefore terminates, and no action for breach of any
such duties may thereafter be commenced. W. R. MEADOWS, INC. shall in no event
be liable for consequential damages. Unless otherwise agreed to in writing, no
warranty is made with respect to materials not manufactured by W. R. MEADOWS,
INC. We cannot warranty or in any way guarantee any particular method of use or
application of the performance of materials under any particular condition.
Neither this Warranty nor our liability may be extended or amended by our
salesmen, distributors or representatives, or by our distributor's
representatives, or by any sales information or drawings.
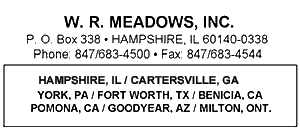
|