| |
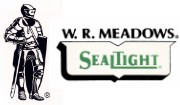
NO. 398
SEALTIGHT®
FUTURA®-15
VERY RAPID-SETTING HORIZONTAL REPAIR MORTAR
DESCRIPTION
SEALTIGHT FUTURA-15 is a one component,
cementitious, very rapid-hardening structural repair mortar designed for
horizontal applications. FUTURA-15 is composed of selected cements, graded sands
and chemical additives. This proprietary blend produces a very rapid-setting
structural repair mortar even in cold weather conditions without the aid of
chloride or gypsum based accelerators.
USES
SEALTIGHT FUTURA-15 is ideal for structural patching of concrete
pavements, bridges, parking decks, airport runways and taxiways. FUTURA-15 is
also designed for repair of industrial floors, expansion joint nosings,
sidewalks and general commercial applications, along with grouting keyways.
FEATURES AND BENEFITS
 | May be top-coated in as little as four hours
 | Very rapid setting/ Decreases turn-around time
 | Rapid strength gain/ Repairs can be opened to traffic
in as little as an hour
 | Shrinkage compensated/ Minimizes cracking and
de-bonding
 | Contains no chlorides/ WIll not promote reinforcing
steel corrosion
 | Contains no added gypsum/ Excellent resistance to
freeze/thaw and wet environments
 | Low permeability/ Protects reinforcing steel from
future corrosion
 | Economical/ Can be extended up to 50% by weight with
aggregrate
 | One component/ Easy mixing, saves labor |
| | | | | | | |
SPECIFICATIONS
Conforms to ASTM C 928-99a "Packaged, Dry,
Rapid Hardening Cementitious Materials for Concrete Repair," Classification
R3, Very Rapid Hardening.
SHELF LIFE
12 months when stored on pallets in a dry, cool
area.
YIELD
 | 50 lb. (22.7 Kg) bag yields yields 0.41 ft.³ (11.6L)
 | Extend with 12.5 lb. (5.68 Kg) of aggregrate - yields
0.49 ft.³ (13.93L)
 | Extend with 25 lb. (11Kg) of aggregrate - yields 0.58
ft.³ (16.4L) |
| |
Yields listed above are based on 4.75 pints (2.25L) of
water per 50-lb. bag and will vary based on substrate profile, mix ratios,
aggregate type and waste. Field trials should be performed to determine yields
based on aggregate type.
TECHNICAL DATA
The following physical properties were determined
using the maximum water to powder ratio of 5.25 pints (2.48L) per 50 lb. (22.7
kg of SEALTIGHT FUTURA-15 at 75ºF (23.5ºC)
Set Time Per ASTM C 191 |
Initial |
14-18 Minutes |
Final |
20-25 Minutes |
Working Time 7-9 Minutes |
Flow Per ASTM C 928¹ |
103% after 5 Minutes |
|
Compressive Strength (at
75º F, 50% RH)
Per ASTM C 109¹ |
at 1 hour |
2,000 PSI (14
MPa) |
at 2 hours |
3,500 PSI (24
MPa) |
at 1 day |
6,000 PSI (42 MPa) |
at 7 days |
8,500 PSI (59 MPa) |
at 28 days |
9,000 PSI (65 MPa) |
|
Bond Strength Per ASTM C 882¹² |
@ 1 day |
2,370 psi (16 MPa) |
@ 28 days |
3,910 psi (27 MPa) |
Modulus of Elasticity
Per ASTM C 469¹ |
5.16 x 106
psi (35.5 GPa) |
Length Change Per ASTM C 928¹ |
Drying Shrinkage³ |
-0.11% |
Wet Expansion |
+0.08% |
Scaling Resistance Per ASTM
C 672¹ @ 25 Cycles |
Visual Rating |
0 Rating – No Scaling |
Mass Loss |
0.00 – No Mass Loss |
Freeze-Thaw Resistance Per
ASTM C 666 (Procedure A)¹ |
At 300 Cycles |
100% RDM4 |
|
All Technical Data is
typical information, but may vary due to testing methods, conditions and
procedures.
¹
Independent Reports Are Available Upon Request.
² Modified – No Bonding Agent used. Pre-dampening of properly
prepared substrate.
³ Cured after 3 hours at 73+/-3ºF and 50+/-4% RH
4
RDM - Relative Dynamic Modulus |
FOR BEST PERFORMANCE
 | FUTURA-15 is recommended for concrete repairs only
 | Do not use as an underlayment or overlay
 | Protect from freezing for a minimum of 24 hours.
 | Do not bridge moving cracks. Extend existing control
and expansion joints through FUTURA-15.
 | For large areas with no control, expansion or
construction joints, refer to ACI Guidelines.
 | Do not exceed a length-to-width ratio of 2 to 1 for the
repair area.
 | Do not add any admixtures.
 | Exceeding liquid requirements shall result in reduced
physical properties.
 | Realize that set time will decrease as the product,
air, substrate and mixing liquid temperature increases and will increase as
the temperature decreases.
 | Repair areas should be saw cut and slightly undercut to
a minimum depth of a 1/2" (12.5 mm). Do not featheredge.
 | Protect from conditions that may cause early water
loss; windy, low humidity, high temperature and direct sunlight. Early water
loss is exasperated in thin applications.
 | Realize that the use of extender aggregate will alter
physical properties.
 | Do not use evaporation retardants, such as SEALTIGHT
EVAPRE with this product.
 | Failure to follow industry standard practices may
result in decreased material performance.
 | Proper application is the responsibility of the user.
Field visits by W.R. MEADOWS personnel are for the purpose of making
technical recommendations only, and are not to supervise or provide quality
control on the job-site. |
| | | | | | | | | | | | | |
SURFACE PREPARATION
Perform surface preparation in accordance
with ICRI Technical Guidelines No. 03730, "Guide for Surface Preparation
for the Repair of Deteriorated Concrete Resulting from Reinforcing Steel
Corrosion." Mechanically abrade existing substrate to remove all unsound
concrete, but do not use excessive force, which may cause micro-fracturing.
Substrate must be structurally sound and free of any contaminants that will
adversely affect the bond. Prepared substrate surface must have a sufficient
profile of ¼" to ensure adequate mechanical lock. Saw cut perimeter of
repair zone to a depth of ½" to avoid feather edging.
Completely expose all reinforcing steel, ensuring a
minimum clearance of ¾" behind reinforcing steel. Abrade entire
circumference of steel to a white metal finish. Perform reinforcing steel
preparation in accordance with ICRI Technical Guidelines No. 03730. Pre-dampen
concrete substrate to a saturated surface dry (SSD) condition. Remove all
standing water and puddles.
MIXING
Mix only complete bags. Using a suitable sized mortar type mixer, add 4.75-5.25
pints (2.24-2.48L) of clean water to the mixer per 50 lbs. (22.7 kg) bag of
FUTURA-15. If extension is required, add appropriate amount of aggregate to
mixer prior to the addition of FUTURA-15. Mix for 3-5 minutes until homogenous
and lump-free. Do not mix more product than can be mixed, placed and finished in
15 minutes at 70° F (21° C). Do not over-mix.
AGGREGATE EXTENSION
For repairs greater than 2" (51mm) in depth; extend FUTURA-15 with 12.5
lbs. (5.68 kg) of aggregate. For repairs greater than 4" (102 mm) in depth
extend FUTURA-15 with 25 lbs. (11.36 kg) of aggregate. The aggregate must be a
minimum of 3/8" (9mm) size, saturated but surface dry condition, clean pea
gravel. Always add the aggregate to the mixing water prior to the addition of
FUTURA-15. For configurations requiring greater than 50% extension or larger
areas, contact your local W.R. MEADOWS representative. Proper stress relief must
be given for large patch areas.
PLACEMENT
Apply FUTURA-15 by trowel or screed. Compact FUTURA-15 well against the prepared
substrate prior to bulk placement. Ensure complete encapsulation of reinforcing
steel. Finish surface by screeding FUTURA-15 to a level surface. For a rough
finish, a broom or burlap bag is suitable, never re-temper. Do not re-temper or
overwork.
Follow ACI 305-R89 "Standard on Hot Weather
Concreting" or ACI 306-R88 "Standard on Cold Weather Concreting,"
when applicable.
May be top-coated with an epoxy-based overlay after 4
hours. For all other systems, wait a minimum of 24 hours prior to topcoating.
Consult appropriate installation guide for the product to be overlaid.
CURING
FUTURA-15 must be immediately cured in accordance with ACI 308. If a membrane
curing compound is used, we suggest using SEALTIGHT 2250-WHITE or SEALTIGHT
1130-CLEAR. On large patches, cure repair zone as work proceeds. Wet curing for
a minimum of one day, followed by a suitable curing compound helps minimize
shrinkage.
SAFETY AND TOXICITY
Avoid inhalation of dust. Avoid direct contact with this product. Utilize gloves
and goggles to minimize direct contact. If contact occurs, wash affected areas
with mild soap and water. Keep product out of reach of children. FOR INDUSTRIAL
USE ONLY. Refer to Material Safety Data Sheet for complete Health and Safety
Information.
This material last updated November, 2001.
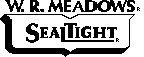
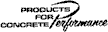
W. R. MEADOWS, INC. warrants that, at the time and place
we make shipment, our materials will be of good quality and will conform with
our published specifications in force on the date of acceptance of the order.
THE FOREGOING WARRANTY SHALL BE EXCLUSIVE AND IN LIEU OF ANY OTHER WARRANTY,
EXPRESS OR IMPLIED, INCLUDING THE IMPLIED WARRANTIES OF MERCHANTABILITY AND
FITNESS FOR A PARTICULAR PURPOSE AND ALL OTHER WARRANTIES OTHERWISE ARISING BY
OPERATION OF LAW, COURSE OF DEALING, CUSTOM OF TRADE OR OTHERWISE. As the
exclusive remedy for breach of this Warranty, we will replace defective
materials, provided, however, that the buyer examine the materials when received
and promptly notify us in writing of any defect before the materials are used or
incorporated into a structure. Three (3) months after W. R. MEADOWS, INC. has
shipped the materials, all our Warranty and other duties with respect to the
quality of the materials delivered shall conclusively be presumed to have been
satisfied, all liability therefore terminates, and no action for breach of any
such duties may thereafter be commenced. W. R. MEADOWS, INC. shall in no event
be liable for consequential damages. Unless otherwise agreed to in writing, no
warranty is made with respect to materials not manufactured by W. R. MEADOWS,
INC. We cannot warranty or in any way guarantee any particular method of use or
application of the performance of materials under any particular condition.
Neither this Warranty nor our liability may be extended or amended by our
salesmen, distributors or representatives, or by our distributor's
representatives, or by any sales information or drawings.
|