| |
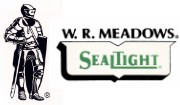
NO. 392
REZI-WELD™
LV 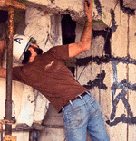
LOW VISCOSITY INJECTION EPOXY
Provides a low-viscosity, easy-flowing
injection epoxy in a unique, unitized package.
SEALTIGHT REZI-WELD LV Low Viscosity Injection Epoxy is a two-component,
easy-flowing, low-viscosity structural epoxy adhesive suitable for pressure
injection of cracks, and as a binder for a wide variety of maintenance, repair
and concrete rehabilitation patching and grouting applications.
Technical Description
SEALTIGHT REZI-WELD LV Low Viscosity Injection Epoxy is 100%
solids, moisture insensitive, very low viscosity, high modulus, and high
strength structural injection resin. REZI-WELD LV is V.O.C. compliant and
resists most chemicals.
REZI-WELD LV features a unique and innovative unitized
packaging concept. It combines two color-coded, pre-measured, components into an
easy-to-handle, single unit along with a handy, wood mixing paddle. The unitized
packaging eliminates mishandling and mismatching of the components on the
jobsite.
Uses
REZI-WELD LV is designed for gravity feeding or pressure injecting
using two-component metering systems, hand-held bulk guns or pressure pots. It
is suiable for injecting fine, non-moving structural cracks for permanent
repairs.
When mixed with sand or aggregates REZI-WELD LV makee an economical, easy-to-use
epoxy mortar for patching or repairing defects in concrete substrates, securing
machinery base plates to concrete floors, interior non-skid pathways and
structural bonding applications.
Advantages and Benefits
 | Ideal for pressure injection and gravity feeding
 | Advantageous as a low viscosity, epoxy adhesive binder
 | Bonds cured concrete, wood, plastic or metal to
concrete
 | Combines with aggregate to form interior non-skid
pathways
 | Resists industrial chemicals as well as impact and
attack from moisture
 | Features low-viscosity, high-modulus, high-strength,
self-leveling characteristics
 | VOC-compliant
 | Furnished in unitized packaging
 | Can be extended with sand for other uses |
| | | | | | | |
Application Tools

Electric Drill with Jiffy Blade |

Injection Pump |

Roller |
Application
SURFACE PREPARATION: All surfaces to be
bonded must be free of standing water and completely clean of dirt, rust, curing
compounds, grease, oil, paint, waxes and other materials which would prevent a
maximum bond.
Concrete should be cleaned by mechanical abrading or
sandblasting to a sound surface. Vacuum or blow dust away with compressed air.
Mechanically abrade metal base plates to a bright metal finish.
Exposed steel surfaces should be sandblasted and vacuumed clean; if not
possible, degrease the surface and use sandpaper or a wire brush to reveal
continuous, bright metal.
MIXING NOTE: Condition all components to 60-85ºF for 24 hours prior to use.
Pre-mix each component. Mechanically mix at slow speed (600-900 rpm) using a
drill and Jiffy Blade or drum mixer to 3 minutes or until completely mixed while
scraping the sides to ensure complete blending of components. Avoid air
entrapment. Mix only very small quantities by hand for a minimum of 3 minutes or
until sufficiently blended together using the supplied stirring stick. Scrape
the sides of the container to ensure complete blending of components. Mix only
the amount of epoxy that can be applied within the product's potlife. Potlife
will decrease as the ambient temperature and/or mass size increases.
INJECTION: Epoxy can be gravity fed into horizontal cracks that are small,
(1/4" [6.35mm] maximum width) and have a limited depth. For large injection
projects, a self-proportioning, mixing and pressure injection equipment is
recommended. For small injection projects, SEALTIGHT REZI-WELD RAPID SET PRE-PAK
self-contained, barrier-type cartridge may be suitable.
INTERIOR, NON-SKID PATHWAYS: For thin applications, apply at a rate not to
exceed 110 ft.² per gallon (2.70m²/liter). For heavy coverage, apply layer of
sand or grit over epoxy and allow to set. Blow excess sand away. NOTE: REZI-WELD
LV IS NOT TO BE USED AS A FINISHED FLOOR COVERING OR PROTECTIVE TREATMENT.
AGGREGATES FOR EPOXY-RESIN MORTARS: Combine clean, dry aggregates with freshly
mixed epoxy in a ratio of 1 part epoxy to 1 to 4 parts, by volume, of graded
aggregates. Patch thickness should not exceed 1-1/2" (38.1mm) per lift.
CLEANUP: Clean tools and equipment immediately with Toluene avoiding heat,
sparks, open flame, breathing vapors or allowing epoxy-containing solvent to
contact skin. Never wash hands with solvent.
Packaging
1 quart (.95 liter) Units
1 gallon (3.79 liter) Units
15 gallon (56.85 liter) Units
Specifications
ASTM C 881, Type I, II, IV and V Grade 1, Class B & C
AASHTO M 235 Type I, II, IV and V, Grade 1, Class B & C
USDA Accepted
Shelf Life
Two years in unopened, damage-free
containers stored in a dry environment between 40º and 95ºF (4º and 35ºC).
Coverage
One gallon (3.8 liter) neat covers approximately 85-110 ft.²
(2.09-2.70 m²/liter) depending on the surface porosity and end use application.
One gallon (3.8 liters) mixed 1:1 with dry aggregate yields approximately 350
in.³ (5.135.45cm³) of grout.
Precautions
DO NOT DILUTE. Mix complete units only. The epoxy must be between
60º and 85ºF (16 and 29ºC) at time of mixing. Warm by placing containers into
hot water. The preferred method is to store the epoxy in a warm room prior to
use. Surface substrate temperature must be between 40º and 90ºF (4 and 32ºC).
Do not seal cracks while under hydrostatic pressure.
REZI-WELD LV is not to be used as an exterior coating as it is not resistant to
ultraviolet rays. This epoxy is corrosive. Personal protective equipment is
necessary. Unused epoxy will generate excessive heat, especially in large
quantities. Unused epoxy should be mixed with dry sand in the container to help
lower the heat. Read and follow application information, precautions and
Material Safety Data information.
Technical Data
Component
Properties |
Resin |
Hardener |
Mix Ratio (PBV=Part
by Vol.)
Appearance
Density, lbs./gal. (kg/liter)
Viscosity, cps
Final Color
Pot Life (1 gal. unit) @ 77ºF (25ºC) |
2 PBV
Clear
9.6 (1.15 kg/liter)
2,000 (mixed)
Light amber (mixed)
40 mins. |
1 PBV
Amber
8.2 (.98 kg/liter) |
PHYSICAL PROPERTIES
Property
7 Day Cure @ 77ºF (25ºC) |
Typical Data |
Test Method |
Tensile
Strength, psi
Elongation, %
Hardness, Shore D
Flexural Strength, psi
Flexural Modulus, psi
Compressive Yield Strength, psi
Compressive Modulus, psi
Bond Strength, psi (2 days)
Bond Strength, psi (14 days)
Absorption, % (24 hours)
Linear Coefficient of Shrinkage |
7,000 (41.4 MPa)
1.6
85
11,000 (75.9 MPa)
52,000,000 (360,000 MPa)
11,000 psi (82.8 MPa)
260,000 (1,800 MPa)
2,500 (17.25 MPa)
3,200 (22.08 MPa)
0.13%
0.004 |
ASTM D 638
ASTM D 638
ASTM D 2240
ASTM D 790
ASTM D 790
ASTM D 695
ASTM D 695
ASTM C 882
ASTM C 882
ASTM D 570
ASTM D 2566 |
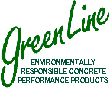
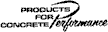
W. R. MEADOWS, INC. warrants that, at the time and place
we make shipment, our materials will be of good quality and will conform with
our published specifications in force on the date of acceptance of the order.
THE FOREGOING WARRANTY SHALL BE EXCLUSIVE AND IN LIEU OF ANY OTHER WARRANTY,
EXPRESS OR IMPLIED, INCLUDING THE IMPLIED WARRANTIES OF MERCHANTABILITY AND
FITNESS FOR A PARTICULAR PURPOSE AND ALL OTHER WARRANTIES OTHERWISE ARISING BY
OPERATION OF LAW, COURSE OF DEALING, CUSTOM OF TRADE OR OTHERWISE. As the
exclusive remedy for breach of this Warranty, we will replace defective
materials, provided, however, that the buyer examine the materials when received
and promptly notify us in writing of any defect before the materials are used or
incorporated into a structure. Three (3) months after W. R. MEADOWS, INC. has
shipped the materials, all our Warranty and other duties with respect to the
quality of the materials delivered shall conclusively be presumed to have been
satisfied, all liability therefore terminates, and no action for breach of any
such duties may thereafter be commenced. W. R. MEADOWS, INC. shall in no event
be liable for consequential damages. Unless otherwise agreed to in writing, no
warranty is made with respect to materials not manufactured by W. R. MEADOWS,
INC. We cannot warranty or in any way guarantee any particular method of use or
application of the performance of materials under any particular condition.
Neither this Warranty nor our liability may be extended or amended by our
salesmen, distributors or representatives, or by our distributor's
representatives, or by any sales information or drawings.
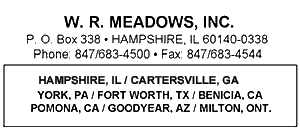
|